CATEGORIES
WPC Board Uncovered: Exploring the Advantages and Disadvantages
Welcome! You've probably heard about WPC (Wood-Plastic Composite) and might be wondering if it's the right choice for your next project. As Allen, from a factory with 7 production lines specializing in WPC Wall Panels and PVC Marble Sheets right here in China, I've seen the rise of WPC board materials firsthand. We export extensively to the USA, North America, Europe, and Australia, working closely with professionals like construction companies, interior designers, and retailers. This article dives deep into the world of WPC, exploring the advantages and disadvantages of WPC. We'll look at what WPC is, how it's made, its applications (especially for floor and cladding), its durability, and how it stacks up against natural wood. Whether you're a procurement officer like Mark Wilson weighing options or an architect seeking innovative building materials, this guide aims to provide the clarity you need to make informed decisions. We'll cover everything from technical specs to practical considerations like cost and maintenance, drawing on real-world experience.
What Exactly is WPC (Wood Plastic Composite)?
So, let's start with the basics. What is this WPC material everyone seems to be talking about? WPC stands for Wood-Plastic Composite. As the name suggests, it's an innovative material used that blends elements of wood fiber or flour with thermoplastics. Think of it as a hybrid material, engineered to capture some of the best qualities of both wood and plastic. The "wood" part usually consists of finely ground wood particles, often sawdust or wood flour, which can come from recyclable materials. The "plastic" component is typically PVC (Polyvinyl Chloride), Polyethylene (PE), or Polypropylene (PP).
This unique combination of wood fibers and plastics creates a composite material that looks and sometimes feels like wood but offers enhanced properties. WPC isn't just one single thing; it's a category of composite boards that can be formulated in different ways depending on the desired application – whether it’s for a deck, floor, cladding, fencing, or even window and door frames. The precise ratio of wood to plastic, along with additives like colorants, stabilizers (for UV resistance), and lubricants, determines the final characteristics of the WPC board.
For professionals in construction and design, understanding WPC is crucial because it presents a versatile alternative to traditional wood in many scenarios. It aims to overcome some common limitations of natural wood, such as susceptibility to moisture, rot, and termite attacks, while still offering a degree of aesthetic appeal. As a manufacturer, we see growing interest in WPC precisely because of this blend of performance and aesthetics.
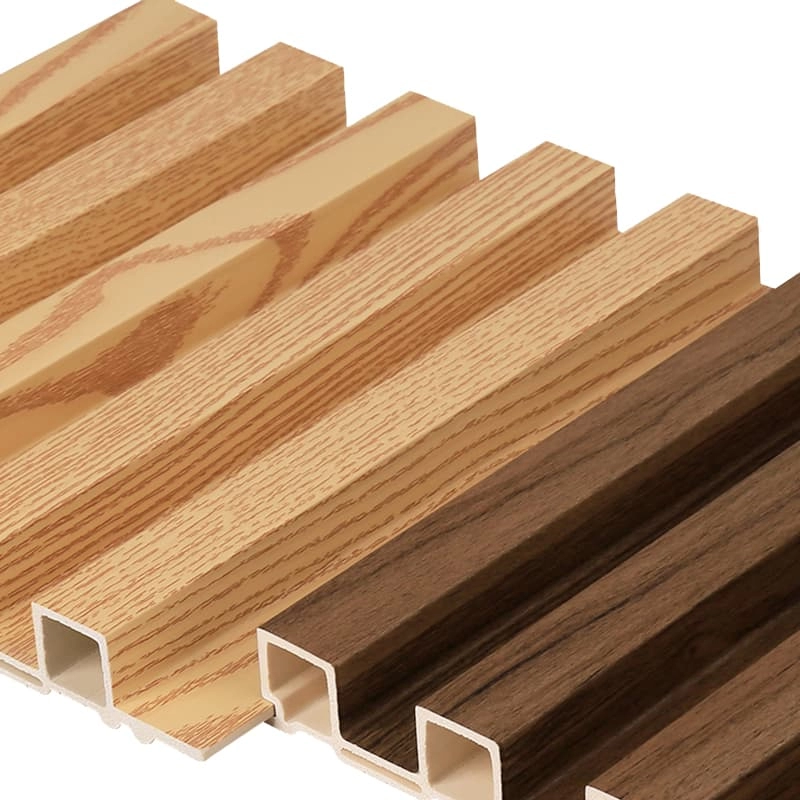
How are WPC Boards Made? Understanding the Composition
Creating WPC boards is quite an interesting process. It's all about precisely combining the right ingredients under controlled conditions. The primary components are wood fiber (or wood flour) and thermoplastics like PVC, PE, or PP. Sometimes, other cellulosic materials might be used as a filler. These raw materials, often including recyclable content, are thoroughly dried and then mixed together in specific proportions. This ratio is critical – it influences the board's final strength, flexibility, and resistance properties.
After mixing, this blend of wood and plastic, along with any necessary additives (like UV inhibitors, pigments for color, binding agents), is typically processed using extrusion or injection molding. Extrusion is very common for products like deck boards, cladding, and profiles for window and door frames. The mixture is heated and forced through a die shaped to create the desired profile of the WPC board. It's then cooled, solidifying into its final form. The surface might undergo further treatment, like embossing to create a wood-grain texture or sanding for a smoother finish.
The goal of this manufacturing process is to fully encapsulate the wood fiber within the plastic matrix. This encapsulation is key to many of the advantages of WPC, such as its moisture resistance and protection against termite infestation. Quality control during this phase is vital – ensuring consistent mixing, temperature, and pressure leads to a highly durable and reliable WPC product. As a factory owner, I can tell you that meticulous attention during production makes all the difference in the final WPC board quality, something discerning buyers like Mark always appreciate.
What are the Key Advantages of Using WPC Boards?
One of the main reasons WPC boards have gained such popularity, especially in markets like the USA and Europe, lies in their impressive list of advantages. Compared to natural wood, WPC boards offer several compelling benefits that resonate with builders, designers, and end-users alike.
Here’s a breakdown of the key strengths:
- Enhanced Durability: WPC is engineered to last. It's resistant to common wood problems like rot, decay, and termite attacks. This inherent durability means a longer lifespan, especially in challenging environments.
- Water Resistance: Unlike natural wood, which readily absorbs moisture, WPC is highly resistant to moisture. This makes it an excellent choice for applications in damp areas like bathrooms, kitchens (think modular kitchen cabinets or bathroom vanities), and outdoor spaces exposed to rain. It won't swell, warp, or deform easily due to humidity.
- Low Maintenance: Forget constant sanding, staining, or sealing. WPC boards require minimal upkeep. Usually, simple cleaning with soap and water is sufficient to keep them looking good. This saves time and money over the product's life.
- Eco-Friendly Aspect: Many WPC products are made using recyclable materials, including reclaimed wood fiber and recycled plastics. This helps reduce the demand for virgin timber, contributing positively against deforestation. Being recyclable itself adds to its green credentials.
- Aesthetic Versatility: WPC boards come in a wide array of colors, finishes, and textures, including realistic wood grain patterns. This allows for significant design flexibility, matching various architectural styles for both commercial and residential projects. You can achieve the look of wood without the associated drawbacks.
- Workability: WPC can generally be worked using standard woodworking tools. It can be cut, drilled, screwed, and shaped much like wood, making installation relatively straightforward. Our WPC Wall Panel products, for example, are designed for easy to install processes.
These advantages of WPC make it a compelling material used for a wide range of applications, from flooring options to exterior cladding.
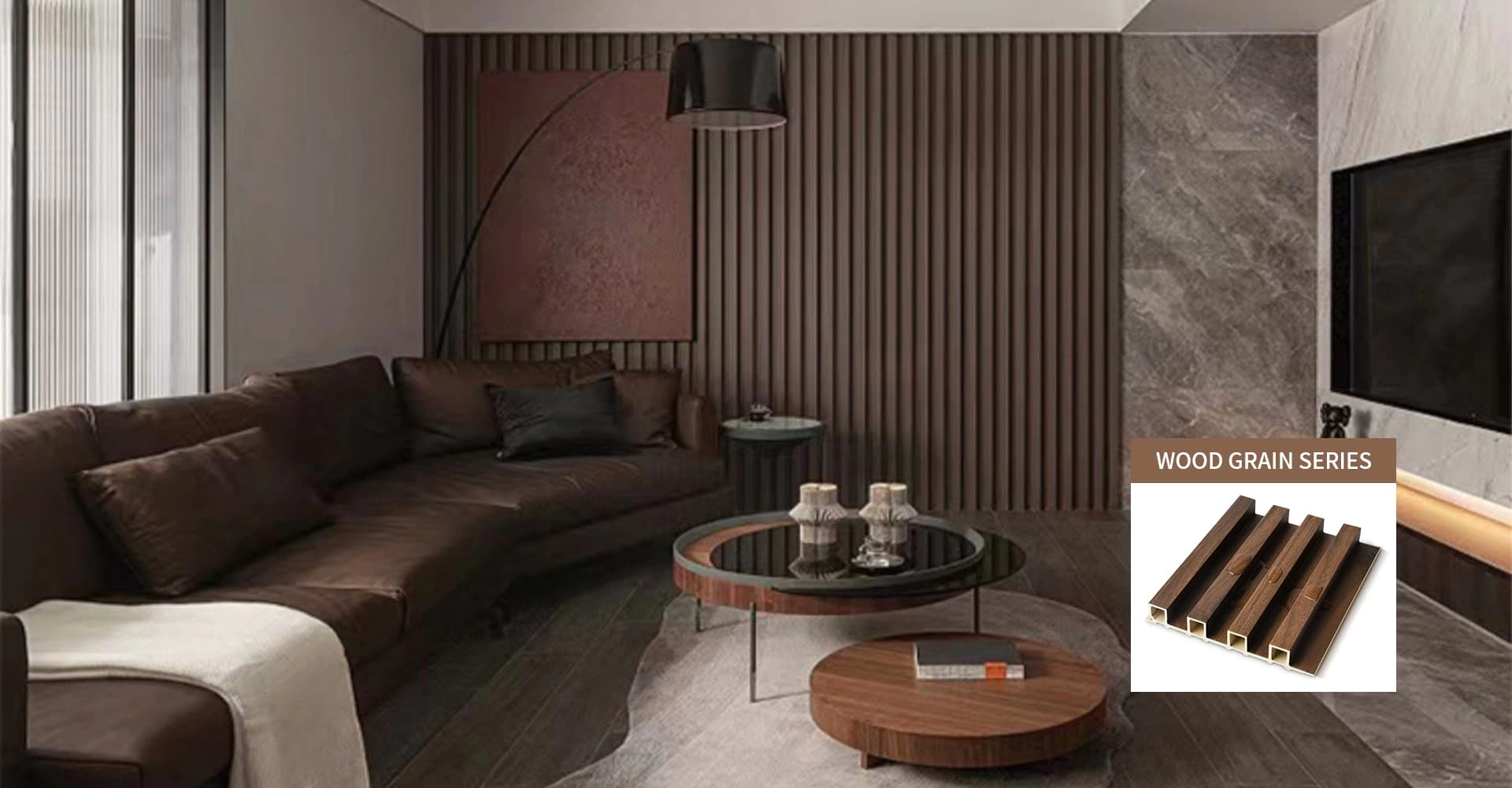
Is WPC Truly Durable? A Look at Longevity and Strength
Durability is a major selling point for WPC, and generally, yes, WPC is a very durable material. Its composite nature provides significant strength and durability. The plastic component shields the wood fiber from environmental factors, particularly moisture and insects like termites, which are notorious for damaging natural wood. This inherent resistance prevents common issues like rot and decay, contributing to a long-lasting performance.
However, the durability of a specific WPC board can vary depending on its formulation and quality of manufacture. The type and percentage of plastic used (PVC, PE, PP), the quality of the wood fiber, and the presence and effectiveness of additives (like UV stabilizers) all play a role. Higher quality WPC boards are engineered to withstand harsh weather conditions, resist fading from sun exposure (UV resistance), and handle physical impacts well. They maintain their structural integrity and appearance over many years, making them suitable for demanding applications like composite decking and exterior cladding.
From my experience supplying WPC globally, I've seen that well-manufactured WPC performs exceptionally well. For instance, our clients often use WPC for floor applications in high-traffic areas or for outdoor structures exposed to the elements. The key is sourcing from reputable manufacturers who adhere to strict quality control standards and can provide documentation for testing and certifications. While no material is indestructible, high-quality WPC offers excellent high durability and longevity, representing a solid long-term investment compared to traditional wood.
How Does WPC Compare to Natural Wood?
This is a question we get a lot, especially from professionals accustomed to working with traditional timber. While WPC often mimics the look of natural wood, its properties differ significantly. Here's a comparative look:
Feature | WPC (Wood-Plastic Composite) | Natural Wood |
---|---|---|
Moisture | Highly water resistant; low absorption | Absorbs moisture; prone to swelling/warp |
Durability | Resistant to rot, decay, termite | Susceptible to rot, decay, termites |
Maintenance | Low; requires cleaning, no staining/sealing | High; requires regular sealing/staining |
Cost (Initial) | Often higher than basic woods | Varies widely; can be lower initially |
Cost (Lifecycle) | Generally lower due to low maintenance | Can be higher due to upkeep |
Eco-Impact | Can use recyclable materials; reduces deforestation | Renewable, but harvesting impacts forests |
Weight | Generally heavier than wood | Lighter (species dependent) |
Appearance | Consistent color/texture; can mimic wood | Natural variations; unique grain |
Workability | Good; uses standard tools | Excellent; traditional material |
UV Resistance | Varies; requires UV inhibitors to prevent fading | Can fade/discolor without protection |
Essentially, WPC is engineered to overcome the inherent weaknesses of natural wood, particularly its vulnerability to moisture and pests. This makes WPC a superior choice for applications where these factors are a major concern, like outdoor deck surfaces, bathroom paneling, or cladding in humid climates. WPC boards offer consistency and predictable performance.
However, natural wood retains its unique aesthetic appeal with natural variations in grain and color that some purists prefer. It's also typically lighter. The choice between WPC and natural wood often comes down to balancing priorities: performance and low maintenance (WPC) versus traditional aesthetics and potentially lower initial cost (natural wood). Many find WPC to be a practical and durable alternative to traditional wood decking and other applications.
Are There Significant Disadvantages of WPC Boards to Consider?
While WPC boasts many advantages, it's important to have a balanced view. Like any material, it has its limitations and potential drawbacks. Understanding the disadvantages of WPC boards helps in making the right choice for a specific application.
Here are some points to consider:
- Initial Cost: WPC products, particularly high-quality composite decking or cladding, can have a higher upfront cost compared to traditional wood options like pressure-treated pine. While the lifecycle cost might be lower due to reduced maintenance, the initial investment can be a barrier for some budgets.
- Weight: WPC boards are generally denser and heavier than natural wood boards of the same dimensions. This can impact transportation costs and might require a more robust supporting structure, especially for elevated decks or certain floor installations.
- Thermal Expansion/Contraction: Like many plastics, WPC can expand and contract with temperature fluctuations. This needs to be accounted for during installation, requiring appropriate spacing (gaps) between boards to prevent buckling or warping, especially in areas with significant temperature swings.
- Appearance: While WPC technology has improved significantly in mimicking wood grain, some people still find that it doesn't perfectly replicate the natural, unique beauty of real wood. The appearance can sometimes be seen as more uniform or "plastic-like," depending on the product quality and finish.
- Potential for Fading: Although many WPC boards include UV inhibitors, prolonged exposure to intense sunlight over many years can still lead to some degree of color fading, particularly in darker shades. The level of UV resistance varies between products.
- Not Structural (Typically): Standard WPC boards are generally not designed for primary structural load-bearing applications like beams or joists. They are typically used for surfacing, paneling, fence posts, or decorative elements.
- Heat Retention: Darker colored WPC products can absorb and retain more heat from direct sunlight than lighter colors or some natural wood types, making them potentially hot underfoot on sunny days.
Considering these pros and cons of WPC is crucial. For buyers like Mark Wilson, weighing these factors against the benefits (like low maintenance and durability) helps determine if WPC fits the project requirements and budget. Sometimes, related products like SPC flooring or PVC Marble Sheets might be considered depending on the specific need (e.g., indoor wall finishes).
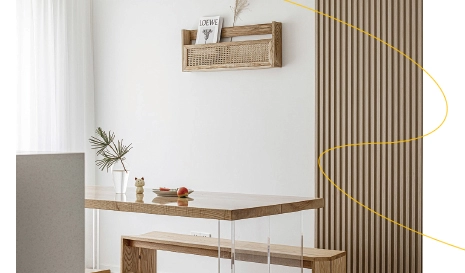
Where Can WPC Boards Be Used? Exploring Applications (Floor, Deck, Cladding)
The versatility of WPC is one of its strongest assets. Thanks to its blend of durability, water resistance, and aesthetic flexibility, WPC boards find applications in a wide range of indoor and outdoor settings, for both commercial and residential projects.
Here are some common uses:
- Decking: This is perhaps the most well-known application. WPC composite decking is a popular alternative to traditional wood decking because it resists weathering, rot, and insects, and requires minimal maintenance. It creates beautiful and long-lasting outdoor space areas.
- Wall Cladding & Paneling: WPC is increasingly used for exterior cladding and interior wall paneling. It provides a protective and decorative layer that can withstand various weather conditions. Our own WPC Wall Panel products are designed for this purpose, offering easy installation and a modern aesthetic.
- Fencing & Railing: WPC is an excellent material for fences and railing systems due to its strength, weather resistance, and low upkeep. It won't splinter like wood and maintains its appearance for years.
- Flooring: While SPC flooring (Stone Plastic Composite) is often preferred for indoor floor applications due to its rigidity, WPC is also used, particularly in areas where moisture resistance is key. Some types of WPC are specifically designed as a flooring option. However, be mindful of potential cons of wpc flooring like susceptibility to heavy scratches compared to SPC.
- Window and Door Frames: WPC profiles are used to create durable and energy-efficient window and door frames that resist warping and moisture damage. WPC doors are becoming more common.
- Furniture & Landscaping: Outdoor furniture, garden sheds, park benches, and landscaping timbers are often made from WPC due to its ability to endure outdoor climatic conditions.
- Interior Applications: Beyond flooring and walls, WPC boards are used for ceilings, modular kitchen components (wardrobe panels, cabinets), bathroom vanities, and decorative trims.
The adaptability of WPC means designers and builders can use a consistent material across different elements of a project, ensuring both performance and a cohesive look.
Is WPC an Eco-Friendly Choice for Building Materials?
The environmental profile of WPC is often highlighted as an advantage, and there's truth to that, but it's nuanced. WPC is generally considered a more environmentally friendly option compared to some traditional materials for several reasons.
Firstly, the manufacturing process often utilizes recyclable materials. The wood fiber component can be sourced from sawmill residues or post-consumer wood waste, reducing landfill burden and the need to harvest virgin timber. This directly helps combat deforestation. Similarly, the plastic component can incorporate recycled plastics (PVC, PE, PP). Using recycled content significantly lowers the environmental footprint of the final WPC board.
Secondly, the durability and long-lasting nature of WPC contribute to its sustainability. Products that last longer require replacement less frequently, reducing the consumption of resources over time. Its resistance to rot and termite damage avoids the need for harmful chemical treatments often applied to natural wood for preservation.
However, it's important to acknowledge the other side. WPC still involves the use of plastics, which are derived from fossil fuels (unless bio-based plastics are used, which is less common). The manufacturing process itself consumes energy. Furthermore, while WPC is often recyclable at the end of its life, the infrastructure for effectively separating the wood and plastic components for high-value recycling is not yet universally established.
Overall, WPC represents a step towards more sustainable building materials, especially when sourced from manufacturers committed to using high percentages of recycled content and efficient production methods. As a manufacturer (Allen here!), we prioritize using eco-friendly practices and recyclable materials in our WPC production lines, understanding its importance to clients worldwide.
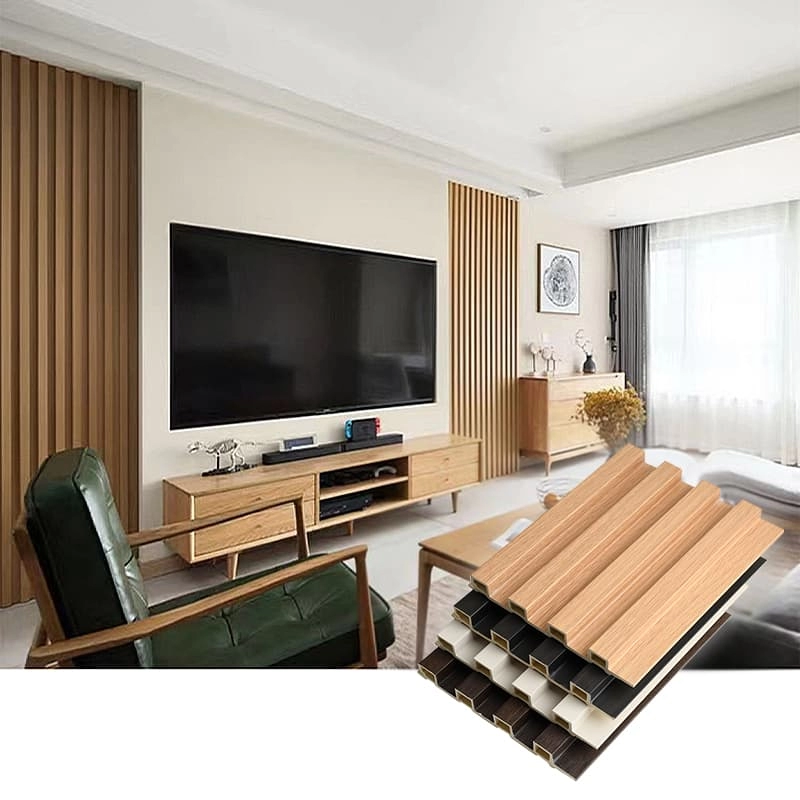
What Should Buyers Like Mark Wilson Look for When Sourcing WPC?
For procurement professionals like Mark Wilson, sourcing WPC boards from overseas suppliers, particularly from countries like China, requires careful consideration to ensure quality, reliability, and value. Based on my experience working with buyers from the USA and other regions, here are key factors they focus on – and rightly so:
- Quality Inspection: This is paramount. Buyers need assurance that the WPC meets specifications for density, strength, color consistency, and dimensional stability. This often involves requesting samples, understanding the manufacturer's quality control processes, and potentially arranging third-party inspections before shipment. Consistent quality across batches is crucial for large projects.
- Certifications: Reputable manufacturers should provide valid certifications. These might include fire safety ratings (e.g., ASTM E84 for the US market), environmental certifications (confirming recycled content or low VOC emissions), and quality management system certifications (like ISO 9001). Buyers like Mark are wary of fraudulent certificates, so verifying their authenticity is important. We ensure our WPC products meet international standards.
- Material Specifications: Clearly define the required WPC formulation. Specify the type of plastic (PVC, PE, PP), the percentage of wood fiber, required UV resistance, and any specific performance characteristics needed (e.g., load-bearing capacity for deck boards, specific fire rating for cladding). Understanding the material used is key.
- Supplier Reliability & Communication: Mark's pain point about inefficient communication is common. Buyers need responsive sales representatives who understand their needs and provide clear, timely updates. A reliable supplier communicates proactively about production schedules and potential delays. Building a trusting relationship is vital.
- Logistics: Smooth logistics are critical to avoid project delays. This includes understanding production lead times, shipping options, port procedures, and ensuring proper packaging to prevent damage during transit. Experienced suppliers can assist with navigating international shipping complexities.
- Payment Methods & Terms: Secure and mutually agreeable payment methods (like L/C or T/T with appropriate milestones) are essential. Clear terms regarding deposits, final payments, and warranties protect both buyer and seller.
- Competitive Pricing: While quality is key, pricing remains a major factor. Buyers seek competitive rates, often achieved by dealing directly with factories like ours, eliminating intermediary markups. However, unrealistically low prices can be a red flag for compromised quality. It's about finding the right balance between cost and value for the WPC board.
Addressing these concerns head-on builds confidence and fosters long-term partnerships, which is our goal at XihongBM.
Why Choose a Factory Direct Supplier like XihongBM for Your WPC Needs?
Working directly with a WPC factory like XihongBM offers several advantages, particularly for volume buyers like construction firms, distributors, and large retailers. As Allen, overseeing our 7 production lines, I see these benefits play out daily for our clients.
Firstly, Cost-Effectiveness: Buying direct eliminates intermediaries and their associated markups. This often translates into more competitive pricing for high-quality WPC boards, allowing businesses like Mark Wilson's to improve their profit margins when supplying WPC floor panels or composite decking to their local markets.
Secondly, Customization & Control: Factories can often accommodate custom orders more easily than distributors. Need a specific color, texture, profile, or length for your WPC cladding or deck project? We have the flexibility to tailor production runs to meet unique specifications, including various WPC wood veneer finishes. This level of control ensures the final product perfectly matches the project requirements.
Thirdly, Direct Communication & Transparency: Dealing directly means clearer communication lines. You can discuss technical details, production schedules, and quality control measures directly with the source. This transparency builds trust and helps resolve potential issues faster, addressing the communication pain points some buyers experience. We prioritize clear, efficient communication with our clients.
Fourthly, Quality Assurance: As the manufacturer, we have direct oversight of the entire production process, from raw material used selection (wood fiber, PVC, etc.) to final inspection. This allows for stringent quality control, ensuring the WPC boards consistently meet high standards for durability, appearance, and performance. We stand behind the quality of our WPC products.
Finally, Expertise & Support: Factory teams possess in-depth knowledge about their WPC materials. We can provide technical support, installation guidance, and insights into the best WPC solutions for specific applications, whether it's for window and door frames, intricate paneling, or heavy-duty flooring options.
Choosing a factory-direct partner like XihongBM ensures you receive high-quality, potentially customized WPC products at competitive prices, backed by direct communication and expert support – crucial elements for success in today's market.
Key Takeaways on WPC Boards:
To wrap up our exploration of WPC (Wood-Plastic Composite), here are the most important points to remember:
- Hybrid Material: WPC combines wood fiber and thermoplastics (like PVC) to create a durable and versatile composite material.
- Major Advantages: Key benefits include high durability, excellent water resistance, low maintenance, resistance to rot and termites, and often uses recyclable materials, making it eco-friendly.
- Key Disadvantages: Potential drawbacks include higher initial cost compared to some woods, heavier weight, thermal expansion/contraction, and appearance that might not satisfy all preferences for natural wood aesthetics. These are the main disadvantages of wpc boards.
- Versatile Applications: WPC is widely used for decking, cladding, fencing, railing, flooring options, window and door frames, furniture, and various interior elements like modular kitchen components.
- WPC vs. Wood: WPC excels in performance and low maintenance, especially in wet or pest-prone environments, while natural wood offers unique aesthetics and can have a lower initial cost.
- Sourcing Matters: When buying WPC, especially internationally, focus on quality inspection, verifying certifications, clear communication, reliable logistics, and finding a balance between cost and value.
- Factory Direct Benefits: Working with a factory like XihongBM can provide cost savings, customization options, direct communication, quality control, and expert support for your WPC needs.
Understanding both the advantages and disadvantages of WPC allows professionals to leverage this innovative material effectively, creating beautiful, long-lasting, and sustainable spaces. Whether you need robust composite decking or stylish interior wall paneling, WPC boards offer a compelling solution worth considering.